Choosing the right soldering equipment for DIP applications is crucial. The Nitrogen Wave Solder offers a reliable solution. Industries like new energy, electronic manufacturing, automotive electronics, and medical devices rely on precise soldering. These sectors demand high-quality connections to ensure product performance and safety. The market for wave solder machines is growing, with an expected value of $236.1 million by 2031. This growth highlights the importance of advanced soldering technologies. For more information, visit https://www.chuxin-smt.com/products/air-wave-solde.
Benefits of Nitrogen Wave Solder
Improved Quality and Precision
Nitrogen Wave Solder enhances solder joint integrity. The use of nitrogen in the soldering process prevents oxidation. This results in stronger and more reliable connections. Consistency in soldering results becomes achievable. Nitrogen ensures uniform heat distribution, which leads to precise soldering outcomes.
Reduced Defects
The Nitrogen Wave Solder minimizes solder bridges and shorts. Nitrogen’s role in the process reduces the occurrence of these defects. Manufacturers experience decreased rework and repair costs. The reduction in defects translates to fewer resources spent on corrections.
Compatibility with Sensitive Components
Nitrogen Wave Solder is safe for heat-sensitive parts. The controlled environment reduces thermal stress on components. Sensitive parts maintain their integrity during the soldering process. The use of nitrogen ensures that delicate components remain unharmed.
For more information on Nitrogen Wave Solder, visit https://www.chuxin-smt.com/products/air-wave-solde.
Technical Aspects of Nitrogen Wave Solder
Role of Nitrogen in Wave Soldering
Nitrogen plays a vital role in wave soldering. Nitrogen prevents oxidation during the soldering process. Oxidation can lead to weak solder joints. Nitrogen ensures that solder joints maintain strength and reliability. The use of nitrogen reduces oxidized solder residues. This reduction improves the overall appearance quality of solder joints. Nitrogen also enhances the solderability of various solder alloys.
Improved wetting properties are another benefit of nitrogen. In a nitrogen environment, the wetting effect of lead-free solder alloys improves. This improvement makes the soldering process more efficient. The wetting properties become comparable to those of lead-containing alloys. Better wetting leads to stronger and more reliable connections.
Enhancement of the Soldering Process
Nitrogen Wave Solder increases solder flow. Increased solder flow ensures that all parts receive adequate solder coverage. Proper solder coverage is essential for creating strong connections. Nitrogen also contributes to better heat distribution. Even heat distribution prevents thermal stress on components. Components remain safe and intact during the soldering process.
The use of nitrogen minimizes soldering defects. Fewer defects mean reduced rework costs for manufacturers. Manufacturers save time and resources by using Nitrogen Wave Solder. The process becomes more efficient and cost-effective. For more information about Nitrogen Wave Solder, visit https://www.chuxin-smt.com/products/air-wave-solde.
Comparison with Other Soldering Methods
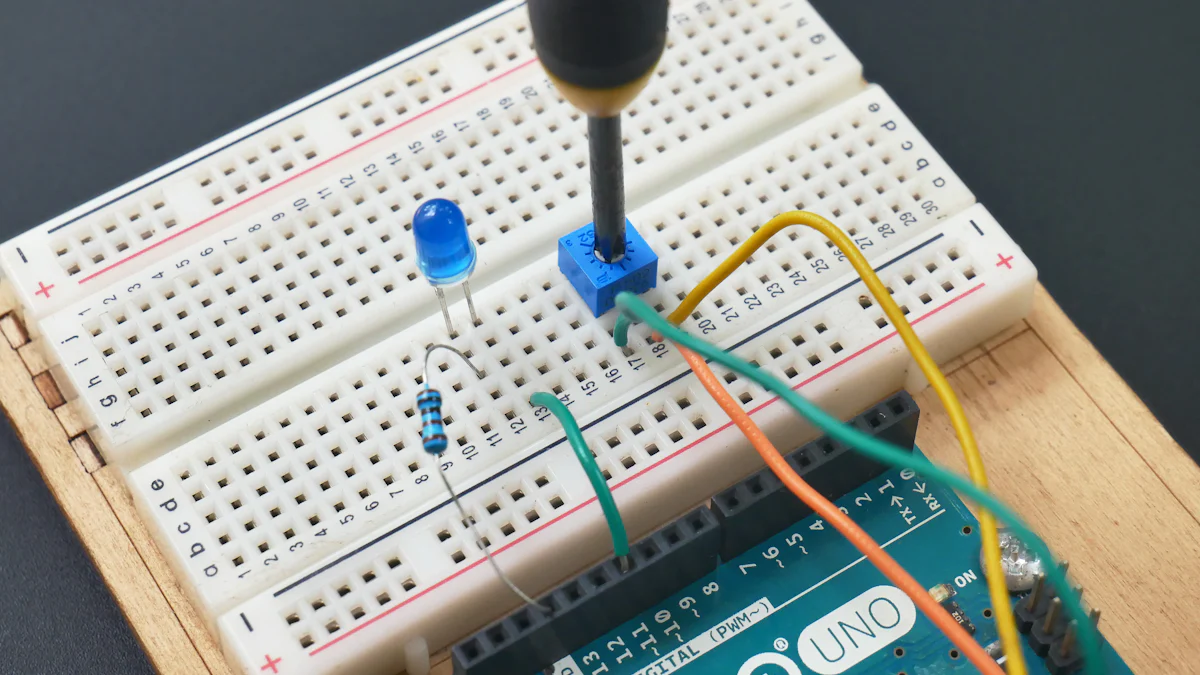
MIG and GMAW
MIG and GMAW serve different purposes in soldering. MIG welding often caters to DIY projects. GMAW suits electronic components due to minimal slag production. Nitrogen Wave Solder offers distinct advantages. Nitrogen prevents oxidation of solder paste and component pins. This prevention improves the wetting effect. Nitrogen reduces oxidized solder residues. Improved adhesion to the board results from nitrogen use.
Other Traditional Methods
Traditional methods lack some benefits. Nitrogen Wave Solder minimizes defects effectively. Reduced rework costs benefit manufacturers. Enhanced solder joint quality becomes evident. Nitrogen improves solder joint strength. Higher consumption of solder and nitrogen occurs in wave soldering. Electrical energy consumption also increases. Despite this, improved appearance quality remains a key advantage.
Consider S&M’s Nitrogen Wave Solder for your DIP applications. The technology offers reliability and precision. Many industries have already benefited from its use. Testimonials from satisfied users highlight the effectiveness. Case studies demonstrate real-world success. Engage with S&M to explore how this solution can meet your needs. Inquire further to discover the advantages for your specific applications.