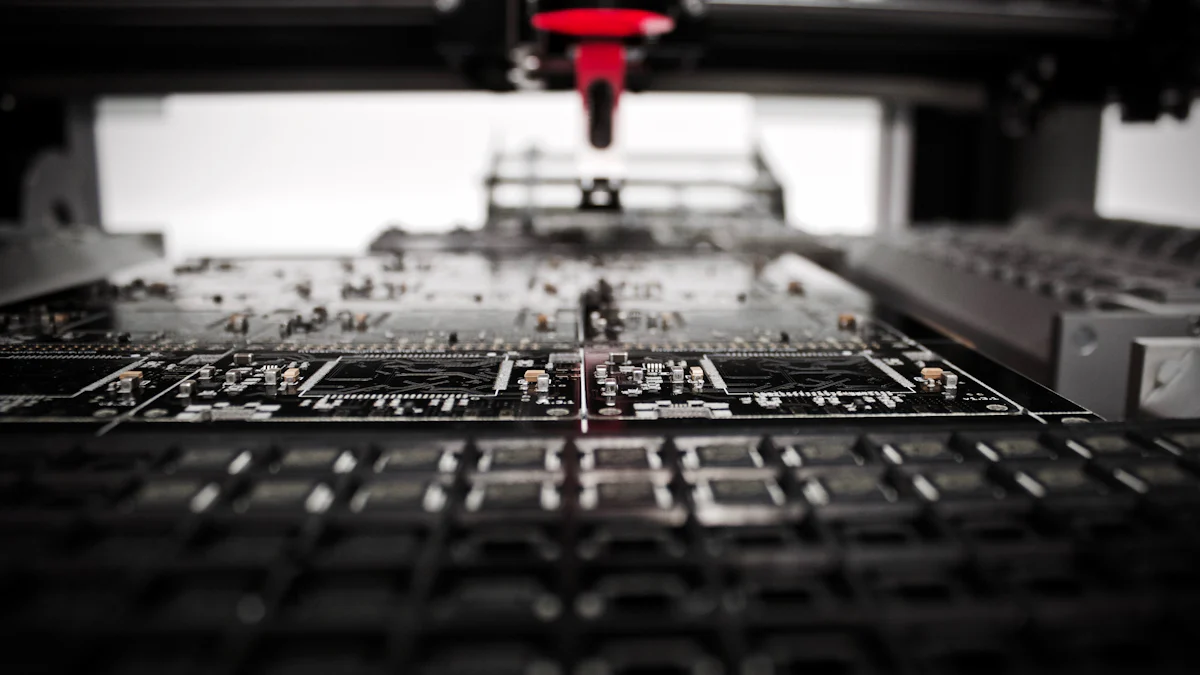
Selective wave soldering is essential in contemporary electronics manufacturing. This technique enables precise soldering of components on printed circuit boards, boosting both efficiency and quality. The global market for selective wave soldering machines is witnessing substantial growth. Industries like automotive, aerospace, and telecommunications are propelling this demand. North America dominates the market, accounting for over 41% of global revenue. Innovative methods in selective wave soldering provide cost-effective solutions, catering to the high-performance requirements of modern electronic components.
Understanding Selective Wave Soldering
Basic Principles
Definition and purpose
Selective wave soldering represents a specialized technique in the electronics manufacturing industry. This method focuses on soldering specific components on printed circuit boards (PCBs) without affecting other areas. The primary purpose of selective wave soldering is to enhance precision and efficiency in assembling electronic devices. Manufacturers use this technique to ensure high-quality connections for through-hole components. Selective wave soldering also minimizes thermal stress on sensitive parts, making it ideal for complex assemblies.
Comparison with traditional wave soldering
Selective wave soldering differs significantly from traditional wave soldering. Traditional wave soldering involves immersing the entire PCB into a wave of molten solder. This process can lead to excess solder usage and potential damage to heat-sensitive components. In contrast, selective wave soldering uses smaller nozzles to apply solder only where needed. This targeted approach reduces waste and conserves resources. Selective wave soldering requires fewer consumables and less maintenance downtime. Manufacturers prefer selective wave soldering for its cost-effectiveness and precision in assembling intricate boards.
Equipment and Setup
Key components of a selective wave soldering machine
A selective wave soldering machine consists of several key components. The system includes a solder pot, which holds the molten solder. A pump creates the solder wave, allowing precise application. Nozzles play a crucial role in directing the solder to specific areas on the PCB. The machine also features a flux applicator to prepare the board surface for soldering. Preheating zones ensure optimal temperature conditions for effective soldering. Each component works together to achieve accurate and efficient soldering results.
Setup process and considerations
Setting up a selective wave soldering machine requires careful planning. Operators must configure the machine to match the specific requirements of the PCB design. Proper nozzle selection is essential for achieving desired soldering precision. The setup process involves adjusting parameters like temperature and solder wave height. Operators must consider the clearance between components to avoid solder bridging. Regular maintenance ensures consistent performance and prolongs the machine’s lifespan. Attention to detail during setup enhances the overall quality and reliability of the soldering process.
Advanced Techniques in Selective Wave Soldering
Process Optimization
Temperature control and management
Temperature control plays a crucial role in selective wave soldering. Precise temperature settings ensure optimal solder flow and adhesion. Manufacturers use advanced sensors to monitor temperatures throughout the process. Consistent heat application prevents thermal damage to sensitive components. Proper temperature management enhances the reliability of solder joints.
Flux application techniques
Flux application techniques significantly impact the quality of solder joints. High-activity flux reduces voids and improves mechanical properties. The Journal of Materials Science highlights the benefits of using high-activity flux. Reduced porosity and enhanced light and heat performance result from effective flux application. Selective wave solder processes benefit from these improvements, ensuring robust connections.
Precision and Accuracy
Nozzle design and selection
Nozzle design determines the precision of selective wave solder applications. Manufacturers choose nozzles based on specific PCB requirements. Smaller nozzles allow targeted solder application, minimizing excess solder. Proper nozzle selection enhances the accuracy of solder placement. This precision is essential for complex electronic assemblies.
Soldering parameters and adjustments
Soldering parameters require careful adjustments for optimal results. Operators set parameters like wave height and speed to match PCB designs. Adjustments ensure proper solder coverage without bridging. Consistent parameter settings improve the efficiency of selective wave solder processes. Reliable solder joints result from meticulous parameter management.
Applications and Benefits
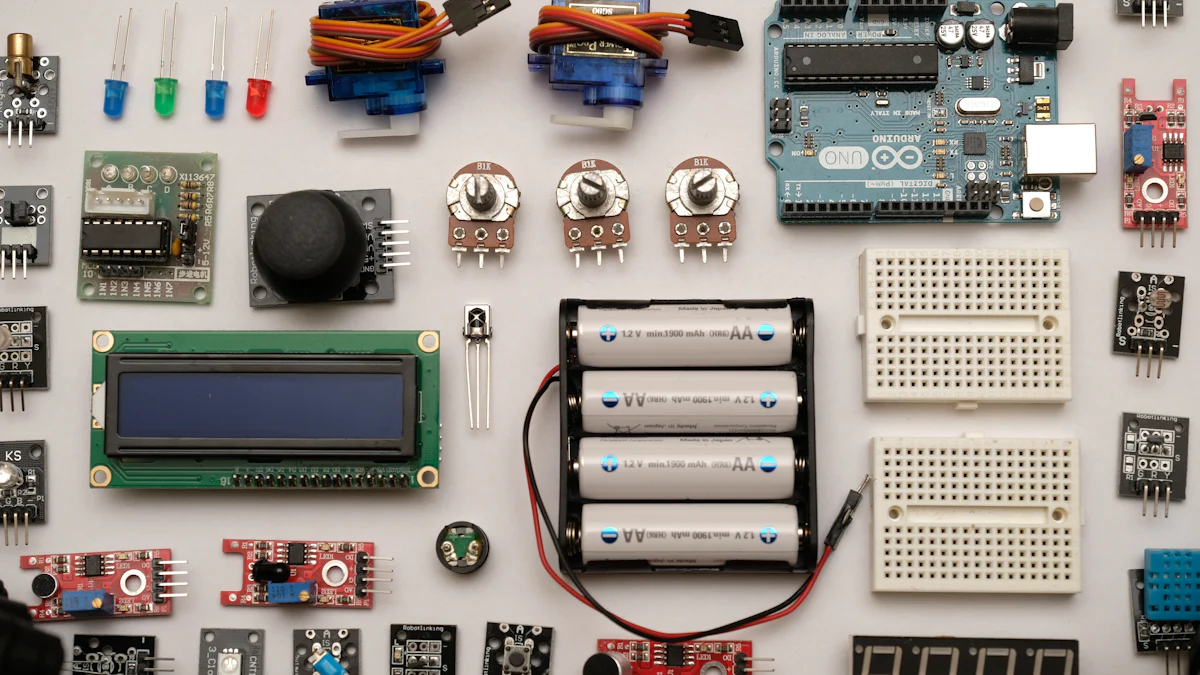
Industry Applications
Use in automotive electronics
Automotive electronics demand high reliability and precision. Selective wave soldering provides the accuracy required for complex automotive systems. This method ensures robust connections for critical components. Automotive manufacturers rely on selective wave soldering for safety and performance. The technique minimizes thermal stress on sensitive parts.
Application in consumer electronics
Consumer electronics benefit from selective wave soldering’s precision. The method supports miniaturization trends in the industry. Manufacturers achieve efficient soldering of densely packed components. Selective wave soldering enhances product durability and functionality. The technique meets the high-performance expectations of modern consumers.
Benefits of Advanced Methods
Improved reliability and quality
Advanced selective wave soldering methods enhance reliability. Precise solder application reduces defects in electronic assemblies. Manufacturers achieve consistent quality with targeted soldering techniques. The process minimizes the risk of component damage. High-quality solder joints result in longer-lasting products.
Cost-effectiveness and efficiency
Selective wave soldering offers cost-effective solutions for manufacturers. The method reduces material waste through precise solder application. Manufacturers experience lower production costs with efficient processes. Advanced techniques optimize resource utilization. The approach increases overall manufacturing efficiency.
Advanced selective wave soldering methods hold immense importance in modern electronics manufacturing. These techniques enhance precision and efficiency, ensuring high-quality outcomes. Industry professionals should embrace these methods to achieve superior manufacturing results. The integration of advanced features like nitrogen inerting and dual soldering pots improves the soldering process. Manufacturers can increase throughput and reduce maintenance requirements. Exploring these advancements offers valuable insights into sustainable practices. Continuous learning and adaptation will drive progress in the field.