“When your PCB has both a 0.3mm pitch BGA and a plastic connector with a temperature resistance of only 80°C, does traditional wave soldering repeatedly put you in the dilemma of “inaccurate soldering” and “burning components”?
Selective wave soldering is becoming the optimal solution for high-mix PCB soldering through the precise control of local tin spraying + nitrogen protection. This article will disassemble how it uses a “millimeter-level scalpel” to solve the five major problems of SMT production.
1)Traditional wave soldering cannot accurately solder high-density boards (such as BGA, and QFN peripheral pins), which can easily lead to bridging or solder leaks.
2)Traditional furnace soldering will heat the entire board, causing heat-sensitive components (such as plastic connectors and LEDs) to deform or fail.
3)Special-shaped boards (such as PCBs with heat sinks) cannot be transferred through the tracks of traditional wave soldering.
4)The traditional wave soldering tin furnace is continuously heated, producing excessive oxidation slag and tin waste (about 20-30% loss).
5))Manual soldering is low-efficient and inconsistent (e.g., the soldering of thick copper layers of power modules).
The Definition of Selective Wave Soldering
Product Major features
Double spray valve, spray valve distance adjustable Independent spray module motion platform, and control system
- High-precision motion control: Using an industrial computer + professional multi-axis motion control card control, can achieve high-precision motion control.
- Complete computer software control: Independent design control software can directly use PCB pictures or GERBER documents for path programming: path start point, welding moving speed, empty travel speed, Z-axis height, wave height, tin collection parameters, etc. can be set on the software.
- Intelligent monitoring system: The machine can automatically monitor and record key process parameters including nitrogen and air pressure, spray flow, preheating time, tin furnace temperature, nitrogen temperature, wave height, liquid level height, and other key process parameters, and the machine has automatic alarm and prompt functions for various common faults.
- Automatic recipe function: The machine comes with a recipe function, which can automatically record the setting of various process parameters to facilitate the saving and recall of product production documents.
- Dual platform precision control: The movement of the flux nozzle and solder nozzle adopts aluminum integrated precision X and Y platforms, with precision ball screw + servo motor transmission, precise control, and high-precision transmission with low noise.
- High-quality transmission structure: The product conveying is driven by their independent stepper motors, which are implemented in two stages, the front section (including the flux spraying section and preheating section) is an aluminum guide rail + imported roller chain conveying structure, and the rear section (solder section) adopts precision stainless steel roller conveying structure, which can realize the stability and accuracy of product transmission.
Welding Process Route
Product Application
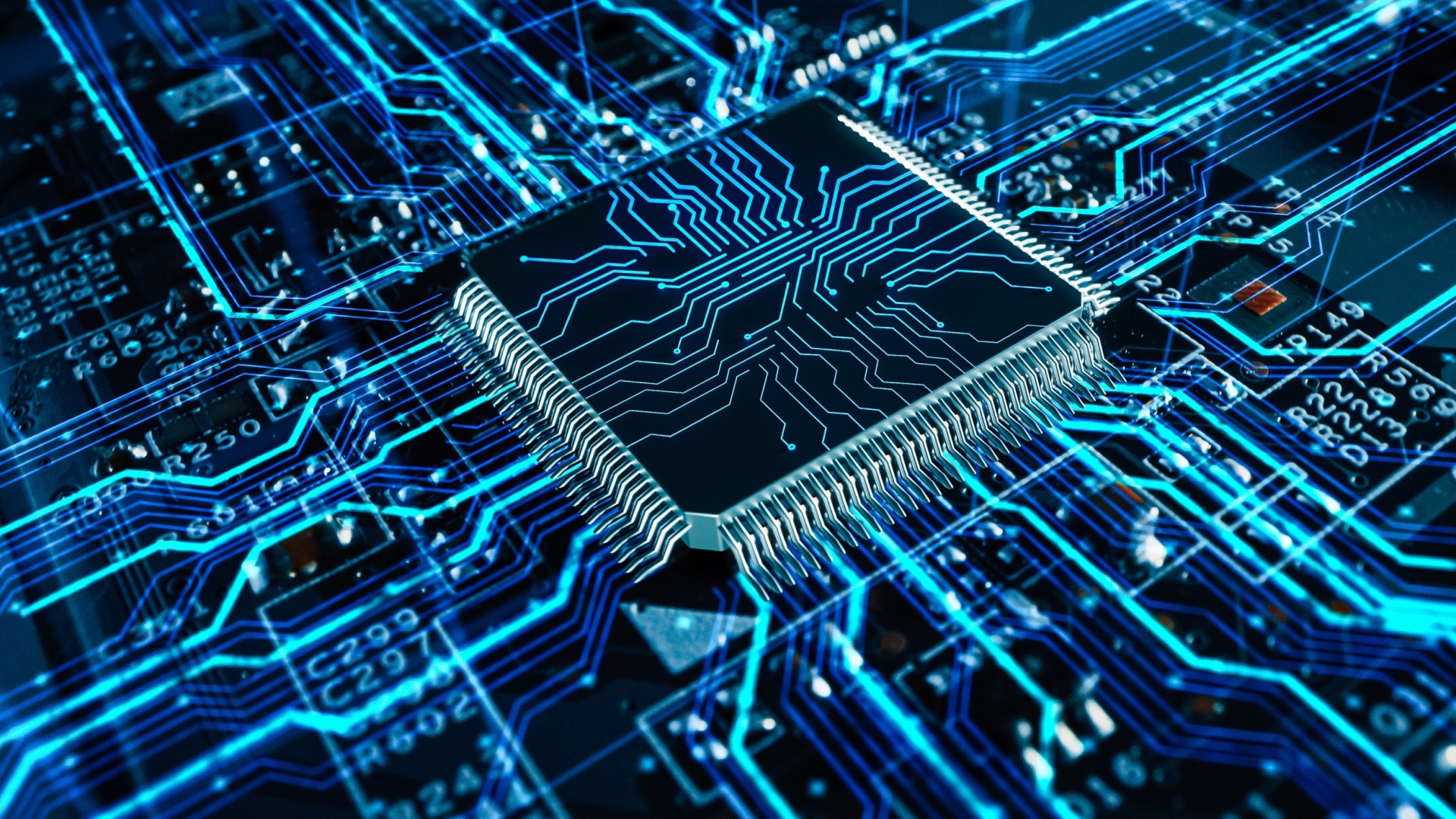
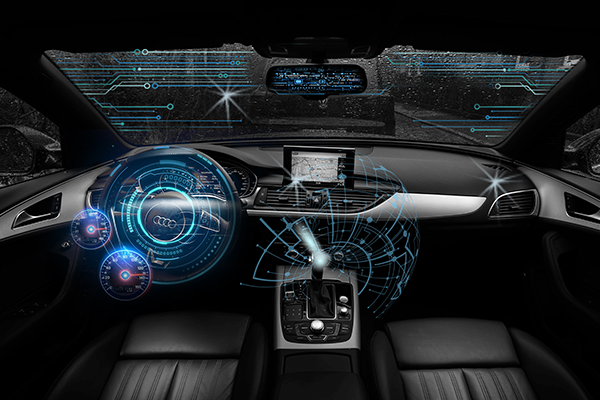
Semiconductor Industry Automotive Electronics