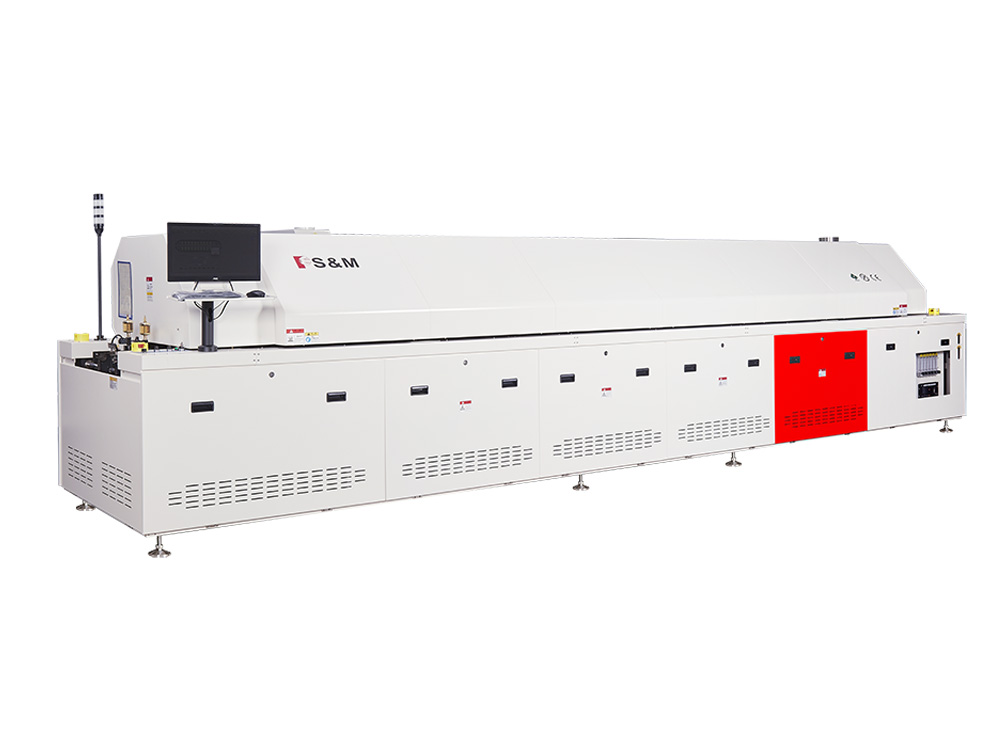
Equipment Definition
Vacuum reflow soldering is a key equipment used in the surface mount technology (SMT) production process. Electronic components are firmly connected to circuit boards through the reflow soldering process. Unlike traditional reflow soldering, the working environment of vacuum reflow soldering is soldering in a vacuum chamber. Its core feature is that it can eliminate bubbles in the solder joints by reducing the air pressure during the soldering process, thereby improving the soldering quality.
Vacuum reflow soldering is generally used in the manufacture of high-reliability products such as automotive electronics, aerospace, power modules, and 5G equipment. These products have very high requirements for air tightness, thermal conductivity, and soldering strength of soldering.
Key Takeaways
- High vacuum with low bubbles, reducing voids in the soldering surface.
- High wettability, improving soldering quality.
- Optimized soldering parameters and processes, enhancing production efficiency.
- Reduce oxidation and reduce the risk of cold solder joints.
Importance of Vacuum Reflow Ovens
- Eliminate solder voids
The vacuum environment of vacuum reflow can effectively reduce the void rate inside the solder joint, which is crucial in high-power devices (such as IGBT modules) or products with high thermal conductivity requirements. Reducing the void rate can improve the thermal conductivity and reliability of welding. - Improve welding strength
Vacuum reflow can ensure full contact between the solder and the pad, making the welding strength higher and avoiding equipment failure caused by pores or bad solder joints. - Optimize welding appearance quality
When welding in a vacuum environment, the surface of the solder joint is smoother and free of pores, meeting the requirements of high-precision and high-reliability electronic products. - Meet the requirements of lead-free welding process
Lead-free solder has a higher melting point and is more likely to form voids. Vacuum reflow has become an important means to solve this problem. - Application in key industries
In SMT lines, vacuum reflow is usually used in manufacturing links with extremely high requirements for welding quality, such as automotive electronic control units (ECUs), medical equipment motherboards, high-frequency communication modules, etc. - Improve product reliability
Through high-precision welding in a vacuum environment, the failure rate of solder joints is reduced, thereby improving the overall quality of the product and extending its service life.
Vacuum Process
Steps involved in the vacuum reflow process
The vacuum reflow process involves several critical steps:
- Preheating: The oven gradually heats the components to a specific temperature to prepare them for soldering.
- Vacuum Application: The PCB is transported through the vacuum reflow rail. Entering the vacuum chamber from the reflow welding zone for vacuum operation.
- Cooling: And flows to the cooling zone for cooling after completion of the operation.
Each step is meticulously controlled to achieve optimal results, making the process highly efficient and effective.
Advantages over traditional methods
- Process Principle
Traditional reflow soldering: mainly heats the air (or nitrogen) for conduction and convection heating to melt the solder and achieve soldering.
Vacuum reflow soldering: adds a vacuum environment to the traditional reflow soldering, exhausts oxygen and moisture in the air by vacuuming, and reduces bubbles and voids generated during the soldering process. - Oxidation Control
Conventional reflow: Nitrogen environment is usually used to reduce the risk of oxidation, but it cannot completely eliminate the occurrence of oxidation.
Vacuum reflow: Oxidation is almost completely avoided through a vacuum environment, thereby improving the quality of welding. - Void Rate
Traditional reflow soldering: More voids may appear inside the solder joint, especially when soldering large-area pads or high-power devices.
Vacuum reflow: The vacuum environment significantly reduces the void rate (can be less than 2%), thereby improving welding reliability, especially suitable for power devices and high-precision applications. - Weld Strength and Thermal Properties
Traditional reflow soldering: Due to the high void rate, the mechanical strength and thermal conductivity of the solder joint may be slightly reduced.
Vacuum reflow soldering: The solder joint density is higher, with better thermal conductivity and mechanical strength, which is conducive to improving the reliability and life of the overall product.
S&M Vacuum Reflow Soldering can meet your needs for reducing void rate and improving solder joint performance during product welding. We pride ourselves on the swift diagnosis and resolution of equipment issues, minimizing downtime and maximizing your production efficiency.