Wave soldering is essential in electronic manufacturing, ensuring high-quality connections in DIP lines. Manufacturers depend on wave soldering for consistent results, as reliability is a top priority in electronics production. Faulty connections can lead to device failures, but wave soldering provides a dependable solution. This method offers precision and efficiency, allowing manufacturers to achieve superior product quality. The technique is crucial for mass production, with consistent solder joints enhancing product reliability. Wave soldering remains a cornerstone in the industry.
Understanding Wave Soldering
Wave soldering plays a crucial role in the production of reliable electronic components. The process ensures consistent and high-quality solder joints, which are vital for the performance of electronic devices. Understanding the wave soldering process and its key components helps us appreciate why it is essential in DIP lines.
The Wave Soldering Process
Preheating Stage
The preheating stage prepares the printed circuit boards (PCBs) for soldering. Preheating gradually raises the temperature of the boards and components. This step minimizes thermal shock and ensures even heat distribution. Proper preheating activates the flux applied to the boards. The activated flux cleans the metal surfaces by removing oxides. This cleaning process enhances the wetting action of the solder.
Solder Wave Application
During the solder wave application, PCBs pass over a wave of molten solder. The solder wave coats the exposed metal surfaces on the bottom side of the boards. This wave forms due to the radiating shape of the molten solder. The solder wave ensures that all component leads receive an adequate amount of solder. This step is critical for achieving strong and reliable solder joints.
Cooling and Solidification
The cooling and solidification stage follows the solder wave application. The PCBs move away from the solder wave and begin to cool down. Cooling allows the molten solder to solidify and form permanent connections. Proper cooling prevents defects such as cold solder joints or bridging. Reliable electrical connections result from well-executed cooling and solidification.
Key Components of Wave Soldering
Solder Pot
The solder pot holds the molten solder used in the wave soldering process. The pot maintains the solder at a consistent temperature. Consistent temperature is crucial for forming uniform solder waves. The composition of the solder, often tin and lead, affects the quality of the solder joints. The solder pot’s design ensures efficient heat transfer and stability.
Conveyor System
The conveyor system transports the PCBs through the wave soldering machine. The system controls the speed and angle at which the boards pass over the solder wave. Precise control of these parameters ensures optimal solder coverage. The conveyor system’s reliability directly impacts the efficiency of the soldering process.
Fluxing Unit
The fluxing unit applies flux to the bottom side of the PCBs before they enter the solder wave. Flux is an alcohol-based liquid that plays a critical role in the soldering process. The flux cleans the metal surfaces and promotes solder adhesion. Proper flux application reduces the risk of defects and enhances solder joint quality.
Why Wave Soldering is Essential in DIP Lines
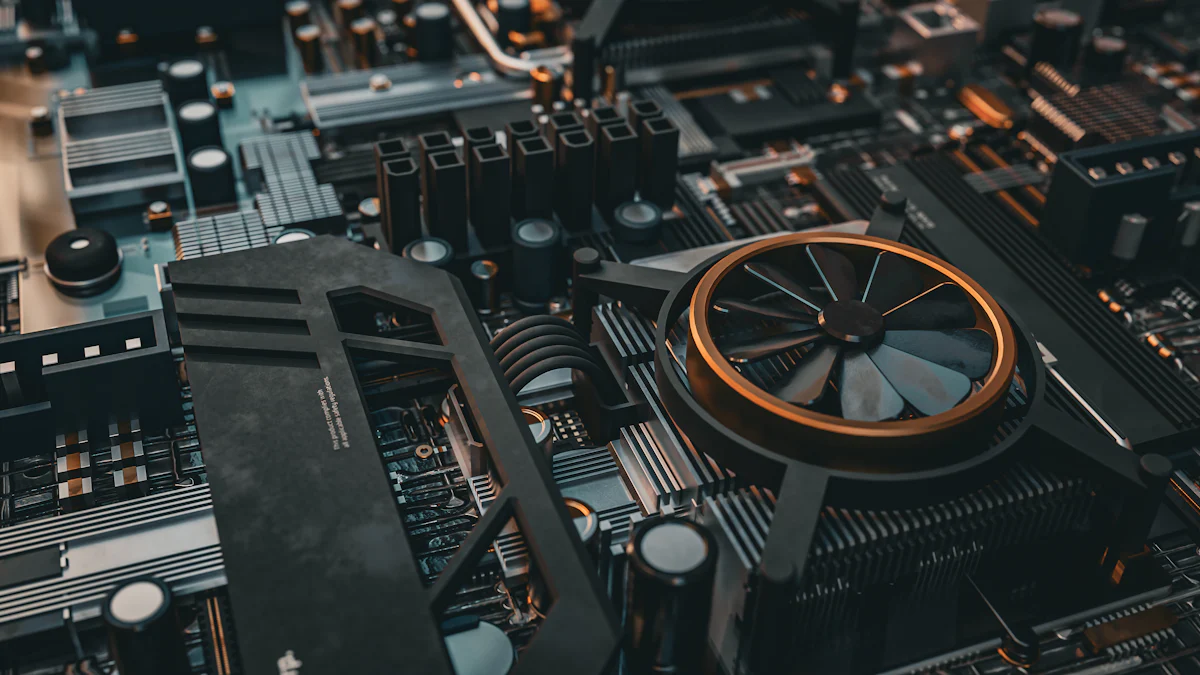
Enhanced Reliability
Wave soldering ensures reliability in DIP lines. Manufacturers achieve consistent solder joints with this method. Consistent joints enhance the durability of electronic components. The process minimizes variations in solder application. Uniform solder distribution prevents weak connections.
Consistent Solder Joints
Wave soldering creates uniform solder joints. Each component receives the same amount of solder. This consistency reduces the risk of electrical failures. Reliable joints support long-term device performance. Consistent joints are crucial for high-precision instruments.
Reduced Defects
Wave soldering significantly reduces defects. The process eliminates common issues like bridging and cold joints. Manufacturers experience fewer reworks and returns. Reduced defects lead to higher customer satisfaction. Quality control becomes more efficient with fewer errors.
Efficiency and Cost-Effectiveness
Wave soldering offers efficiency in production. The process supports large-scale manufacturing needs. High throughput and reduced labor costs make it cost-effective. Industries like healthcare and telecommunications benefit from this efficiency.
High Throughput
Wave soldering enables high throughput in production lines. The method handles multiple PCBs simultaneously. Fast processing speeds up manufacturing cycles. High throughput meets the demands of mass production. Industries rely on this efficiency for timely delivery.
Lower Labor Costs
Wave soldering reduces labor costs. Automation minimizes manual intervention. Fewer workers are needed for soldering tasks. Lower labor costs increase profit margins. Companies invest savings into innovation and development.
Comparing Wave Soldering with Other Methods
Wave soldering remains essential in the electronics industry. Understanding how wave soldering compares to other methods reveals why it stands out. The comparison highlights the advantages and limitations of each technique.
Wave Soldering vs. Hand Soldering
Speed and Precision
Wave soldering offers unmatched speed. The process handles multiple printed circuit boards (PCBs) at once. Automated systems ensure precision in solder application. Hand soldering requires individual attention to each component. This manual method lacks the speed of wave soldering. Consistency becomes a challenge with hand soldering. Wave soldering provides uniform results across all joints.
Suitability for Mass Production
Wave soldering excels in mass production environments. The method supports large-scale manufacturing needs. High throughput meets industrial demands efficiently. Hand soldering suits small-scale or custom projects. The manual approach limits its use in high-volume settings. Wave soldering ensures reliability in DIP lines with consistent quality.
Wave Soldering vs. Reflow Soldering
Application Differences
Wave soldering targets through-hole components. The process is essential for DIP lines. Reflow soldering focuses on surface mount technology (SMT). Each method serves different applications. Wave soldering ensures strong connections for through-hole parts. Reflow soldering suits compact and densely packed PCBs. Both methods have distinct roles in electronic assembly.
Cost Implications
Wave soldering proves cost-effective for high-volume production. The method reduces labor costs through automation. Reflow soldering involves higher initial setup expenses. Equipment and materials for reflow can be costly. Wave soldering remains essential for cost-efficient manufacturing. Industries benefit from the reduced operational costs.
Wave soldering continues to play a vital role in electronic manufacturing. The method’s efficiency and reliability make it indispensable. Comparing wave soldering with other techniques underscores its importance. The process ensures high-quality outcomes in DIP lines. Wave soldering remains a cornerstone in achieving reliable electronic products.
Applications of Wave Soldering in Industry
Wave soldering plays a pivotal role in the electronics industry. The method ensures reliable and efficient soldering for various applications. Industries rely on wave soldering to meet production demands and maintain high-quality standards.
Common Use Cases
Consumer Electronics
Consumer electronics benefit greatly from wave soldering. Manufacturers use this technique to produce devices like smartphones, tablets, and laptops. Wave soldering provides consistent and reliable connections for electronic components. This reliability is crucial for consumer satisfaction and product longevity. The process supports large-scale production, meeting the high demand for consumer electronics.
Automotive Industry
The automotive industry also relies on wave soldering. Vehicles contain numerous electronic systems that require robust connections. Wave soldering ensures these connections remain stable under various conditions. The method supports the production of control modules, sensors, and other critical components. Automotive manufacturers trust wave soldering for its efficiency and reliability.
Future Trends
Technological Advancements
Technological advancements continue to enhance wave soldering. Innovations improve the precision and efficiency of the process. New materials and techniques reduce defects and increase throughput. Automation plays a significant role in these advancements. Automated systems streamline production and reduce labor costs. The future of wave soldering looks promising with ongoing technological progress.
Environmental Considerations
Environmental considerations drive changes in wave soldering practices. The industry seeks to reduce the environmental impact of soldering processes. Lead-free solders and eco-friendly fluxes gain popularity. These materials minimize harmful emissions and waste. Manufacturers adopt sustainable practices to meet environmental regulations. Wave soldering adapts to these changes, ensuring a greener future for the industry.
Wave soldering plays a crucial role in ensuring reliability in electronic manufacturing. Manufacturers rely on this method to achieve consistent and high-quality connections. The process proves essential for maintaining the integrity of DIP lines. Wave soldering enhances product durability and minimizes defects. This technique supports mass production with efficiency and precision. The electronics industry continues to benefit from wave soldering’s essential contributions. Understanding why wave soldering remains indispensable helps us appreciate its value in producing reliable electronic components.